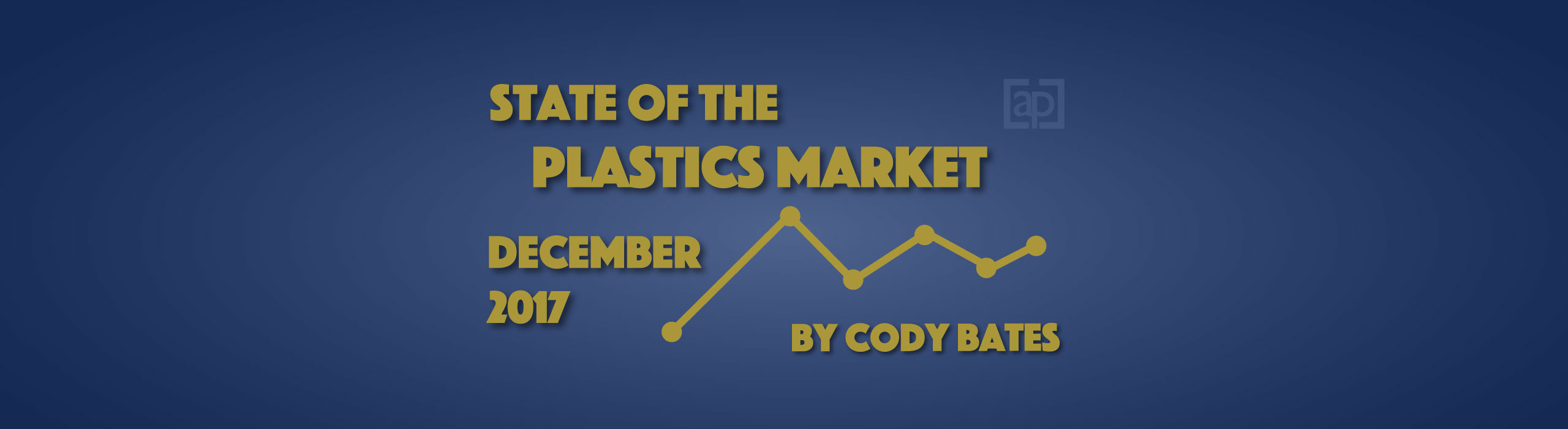
State of the Plastics Market for December 2017
I hope that you had a great Thanksgiving Break and didn’t eat nearly as much turkey as I did. I still have a bit of a tryptophan hang over, but I’m already looking forward to next year. It is my favorite holiday meal of the year by far.
The plastics market is still in a bit of a hangover too.
Polyethylene (PE)
Polyethylene is still really feeling the hurricane effects. While most plants are fully back up online, and ethylene monomer has been brought back up to pre-hurricane levels, all of the down time has left some major holes in some product lines.
As polyethylene producers come back up from a shutdown, they all kind of follow the same formula: they start with homopolymer high density polyethylene (HDPE) materials like milk bottle resin (.7 melt .960 density) and crate grade (8 melt, .960) which are the higher end of the densities. As they check to make sure everything is working, they start to produce more copolymers and work down the density scale. They normally do this with lower flow materials and then lastly, work into the higher melt materials like 10-20 melt resins. We have seen some crate grade type material back on the market, but have yet to see much in the way of .950-.953 materials, especially in high melt injection or low melt film grade resins. We believe most of that is going to be starting at any time, and then work forward.
What all of this means is that we should continue to see higher prices on the higher melt polyethylene, but do expect to see some better numbers on the lower melt materials as more material becomes available. Because the prices have been so elevated, I’m not sure if we are going to see the normal beginning of the year price increases due to demand. I feel that the increase in material supply is going to offset the increase in demand, and prices will probably hold close to what you are currently paying through at least January. At that point, I do expect so start to see some real decreases as the PE market regains its sanity.
Don’t buy heavy at the very first of the year if you can help it. Prices should come down.
Polypropylene (PP)
The polypropylene market got back to a normalized state much faster than the Polyethylene market, but it hasn’t dropped in price due to all of the supply coming off the market during the storm.
As we are going into a bit slower running season for molders currently and everyone wants to get their inventory down as low as possible, I see the stock that producers are able to make coming up a bit and helping to feed the beast again. Like polyethylene, I think that polypropylene is going to follow the same pricing trends. I don’t believe it is going up, but unless there are an end of the year deal or two, I don’t see it falling until sometime in the first quarter.
I know the prices in the beginning of January are going to be higher than they will be in March but, I can’t tell when that tipping point will happen. Try to buy accordingly.
Polystyrene (PS)
The polystyrene market has been up as well, and continues to climb with $.04-$.06/lb added this month alone. Polystyrene is a bit more isolated because of a smaller overall producer base than polyethylene and polypropylene, but along with the storm shocks, the price of oil has been hitting polystyrene more than the other two as well.
Demand is up for PS as the economy is doing well, and I would not be surprised to see it grow a bit more in January as demand picks up. The open market for polystyrene is pretty bare as far as supply goes.
Acrylonitrile butadiene styrene (ABS)
ABS has been somewhat in the same market as PS, but with one exception, we have seen a lot of imported ABS coming in, and this is causing erosion in the ABS price.
Yes, there have been individual producers who have been going up at different times on ABS, but overall, if you have an open window that you can use various grades of ABS in a simple application, there are opportunities to save right now with end of the year deals as brokers and distributors are looking to cut inventory.
Polycarbonate (PC)
Polycarbonate continues to be tight for many grades, especially the extrusion grades. It also seems that there are some of the more specialty grades of materials, optical, medical, etc, where the lead times have really been pushed out far with no signs of them coming back.
It seems that since we are over a year out right now from the Sabic debacle that extremely long lead times are somewhat becoming the norm and not the exception for polycarbonate, and everyone seems to be OK with it.
Nylon
Nylon prices are up based off of feed stock cost/supply issues (what’s new?) and DuPont holding the line on prices from its $.14/lb increase that went into effect in October.
Even the cost of reprocessed and utility grade materials are being lifted up by this tide.
I know that nylon prices are going to hold, at least at this level, through the first quarter, if not increase slightly.
Acetal
While there is still a bit of softness and sloppiness in the price of all copolymer acetals, demand and prices for homopolymer acetal is definitely holding firm.
DuPont was matched in its $.08/lb increase from October and with only 2 real players in that market, it’s not going down any time soon.
I think that it might actually inch up going forward, as demand goes up during the spring pool and construction season.
Final Thoughts
With consumer confidence up, I believe that this is going to be a great 2018 for the plastics business. Many of my customers are running at or near capacity. The “off-shoring” of molding jobs continues to shrink and it looks like we should continue this run through next year.
Please let me know if you need any more information or help.
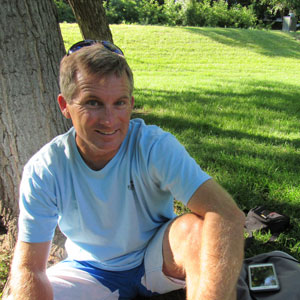
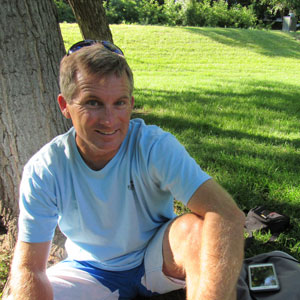
Cody Bates
Plastics Broker
betterthancody@gmail.com
19 years in plastic distribution
18 ½ years of material specification, part designing, good advice, saving tons of money for customers, and solving plastics issues
Motto for the industry “The more information you have, the better you are at what you do. In plastics, the 10,000 hour rule totally applies, and may not be enough hours.